I am a development engineer and in March I had my first trip offshore to install equipment which I had designed. This is a record of my experience.
My initial task was to design a fibre optic wellhead outlet suitable for 4 fibres. This was a particularly interesting project for me because our customer (READ) wanted the design to be 3rd party and tested to PR2, which involves pressure and temperature cycling.
The purpose of a wellhead outlet is to safely terminate electrical or fibre downhole cables into an ATEX (hazardous area) outlet and connect an armoured surface cable to it so that you can have a safe signal running from downhole to surface equipment, usually for downhole sensor applications.
Following the successful testing we were asked to provide a training school to demonstrate the correct installation procedure for both the fibre outlet I had designed and an electrical outlet my colleague had designed. This was to be directly proceeded by a Systems Integrations Test (SIT) at AnTech in which the rig operator would be present so the pressure was on to get the installation slick in a few days.
We held the training school and SIT over 3-4 days which, except for a few tooling issues and fibre splicing delays, went very smoothly and we had two seamlessly installed outlets. So far, all had gone pretty much to plan.
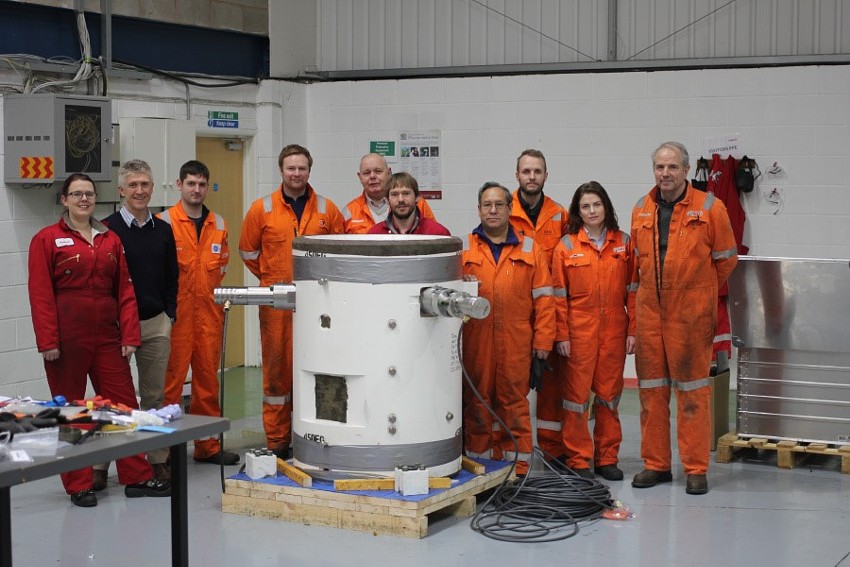
It was towards the end of this week that some of the guys from READ started talking about how useful it would be to have a person from AnTech join them offshore for the installation. Our sales manager asked if I would be prepared to do this and I laughed and said yes I would be more than happy to help with the installation offshore. At that point, however, I really did not think they would take me up on my offer.
A few weeks later I found myself in Aberdeen (my first encounter with Scotland) on a Minimum Industry Safety Training (MIST) and Basic Offshore Safety Induction & Emergency Training (BOSIET) course. This was equal parts fun (with practical drills on fire fighting and helicopter ditching) and petrifying (with horror stories and life raft training). I left feeling confident I could cope during an emergency offshore whilst praying I would never have to apply any of this training in real life.
Before heading out I was a mixture of nervous and excited. I kept running through situations in my head; what if the helicopter had to ditch? What if I inadvertently broke one of the off-shore rules? Or worse still, what if the outlet I had designed didn’t go together as planned and I became the girl who tried but failed on the rig?
Putting these fears aside I donned my survival suit and life jacket, and took a helicopter ride to the platform. I had to wear a green hard hat and arm band to show everyone I was a newbie and people were very friendly and helpful. I was escorted to the jack up rig and inducted with numerous forms to sign, 4 videos, a talk with the OIM (Offshore Installation Manager) and medic and a grand tour of the rig. It was in the galley (canteen) section of the tour that I met Hans, one of the customers I was helping with the installation. This, I believe, was the turning point at which the nervousness subsided and I began to relax a little.
I’d managed to land in time for dinner and, the travel sickness subsiding, I sat down with my new team to a meal of steak and chips. I must be fair; the food was good. Although it was not quite the gourmet selection many of my colleagues assured me it would be, what they lacked in quality, blimey did they make up for it in quantity! It was possible to eat 3 cooked meals per day. If, at the morning break, your 6 o’clock fry up hadn’t quite sated your appetite, they bought out trays of hot bacon and sausage baps to the boot shack. In the afternoon, a selection of cakes and biscuits littered the table – needless to say my diet was postponed for this week.
My first few days became a blur, after performing an inventory on the parts and phoning our production team to be told that “yes the redress kits are in the bag, if you open it up…” it became a waiting game. I mostly helped READ with their preparations, for instance planning the installation of the server rack that the fibre would terminate into. This took me by surprise as I had not previously thought about where the surface cable would terminate. Once it was attached to the wellhead that was it, surely? In fact, they had a 6ft server rack, including pull out laptop-style screen and keyboard, and an enormous processor and 8 hard drives to store all the data!
Finally, we were told the wellhead was ready for the two outlets to be installed (a third AnTech outlet had already been installed by the Downhole Gauge Company on the previous shift). Once the downhole lines had been pulled through, a member of the Wellhead Company installed the Grafoil® plugs on both the fibre and electrical lines to secure them to the wellhead. Following this, the fibre optic line was prepared; this involved READ carefully stripping back over 1m of the 1/4” tubing and leaving the 1/8” tubing (containing the fibre) intact. One thing which shocked me during the first few hours of the installation was discovering that the wellheads move. I had always assumed they were completely fixed in place, but in reality they rock slightly with the motion of the sea below.
After lunch, we continued the fibre installation and the flange and autoclave seal assembly were successfully installed. Following this, a pressure test was performed on the first fibre adaptor. Once the fibre unit was ready to be spliced (this is the process of fusing the uphole/downhole fibres together), we split into two teams; working on the electrical and fibre units in unison. With considerably less space for the fibre unit, the first difficulty encountered was that the 1/8” tubing could not be pulled off straight meaning it took longer to prep the fibre line for splicing.
The remaining 4 pressure tests (electrical cable head, electrical flange, second fibre adaptor and fibre feedthru) all passed first time. Following the successful pressure tests the electrical unit was completed except for the cable gland installation as this would be completed by the platform maintenance team on the morning shift. The fibre outlet was completed during the night shift.
I really enjoyed my time offshore and it gave me a much greater appreciation of some of the difficulties of the equipment installation on a rig. Exposure to the elements and the cramped working spaces accessed via ladders are not what I usually experience when I test outlets in our workshops! It was fantastic for me to be able to see the project through completely from initial design through to offshore completion, and to participate in the offshore installation on the spot problem solving.
Author: Sophie Harris